Lean Six Sigma Curriculum for Augusta High School Students of Georgia
Contact Us
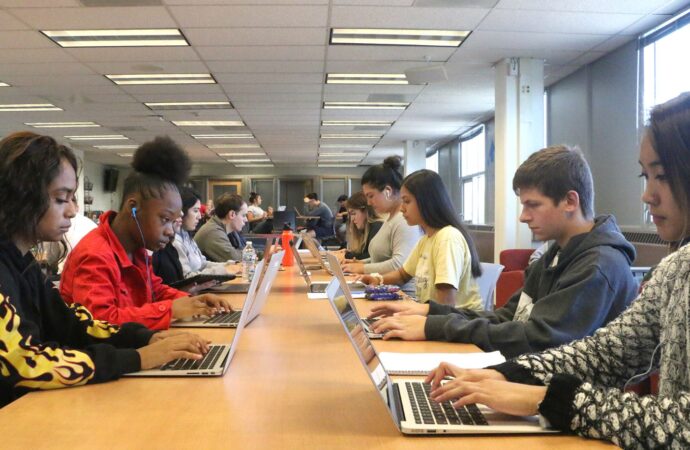
It can take a long time to find the right strategy or methodology to help individuals and companies improve their operations, as many seem to work similarly. Still, others will prove to be more efficient and effective. Then, which one should you go for? Everyone wins when Lean Six Sigma is implemented and even learned as companies obtain the benefits of working with the methodology while practitioners boost their careers with all the knowledge acquired. Lean Six Sigma Curriculum for Augusta High School Students of Georgia is here to assist you with all the details, training, and certification so you can reap all LSS benefits.
You may be familiar with this method because it was developed in the USA, and when focusing on the simple basics of it, it is a way to help companies and manufacturers with their operations. It is not well-known that it can help students and workers to improve their lives, but we have learned that everything depends on the usage and how structures and principles are adapted to the situation.
We want you to be able to understand the implications of investing in it before you decide to do so, as we understand that jumping right away could be too daunting for some.
The main goal of the methodology is to improve the performance of a company’s processes. However, it has a unique aspect that can be applied to any industry: the DMAIC structure. Students and professionals are allowed to learn new skills and use them to their advantage, along with the structures learned with them that can help determine problems and find solutions to their personal projects and ideas.
Lean 6 Sigma is not focused on a single issue or problem. This is the first reason it has such a high value. It addresses multiple issues simultaneously, so people can address the most important while also focusing on ongoing improvement.
What’s the first step in using this methodology?
It is important that you are able to learn it in a way that makes you useful to your employer or institution but also a great asset for yourself as you won’t need to rely on others for your own projects.
The right company should be able to teach you how to implement LSS in different situations depending on your needs and based on the personal growth you’re trying to achieve.
Lean Six Sigma Curriculum Pros of Augusta is here to help you understand this methodology. We don’t offer solutions or services. We would rather walk you through Six Sigma, explain the benefits, and help you make informed decisions thanks to our experts.
Why Should People Learn Lean Six Sigma?
There are many process improvement techniques that can be used to make you a valuable asset for any company or industry you work for, or maybe just to achieve personal growth and obtain career advantages.
Out of all of them, why would you choose LSS when some are more popular among individuals and businesses?
Because most methodologies tend to work for companies alone and don’t offer the individual more than just a way to obtain a new job in specific fields or industries.
However, with LSS, even if your approach is more individual-based, you can still get solutions and implement structures. You don’t have to depend on an organization or business to reap the benefits of Lean Six Sigma.
It is an opportunity to improve the performance of any company, college, high school, or other entity and to identify and address issues that impact efficiency and productivity.
Let’s suppose you have serious efficiency and production problems. Lean Six Sigma can help you to identify and fix these problems and then focus on the most important areas.
But what about the individual? Six Sigma is not just a process. It’s about creating more opportunities for employees, increasing their value, and gaining benefits that can apply to all industries.
You will be able to improve your professional and personal lives by learning about leadership, problem-solving, and decision-making.
You can apply the skills and knowledge that you have acquired during training for any company or personal project to grow.
What Are the LSS Benefits You Can Reap for Yourself?
There are many benefits to this method that go beyond those we discussed previously. We need to look at the benefits for each side—companies, and individuals—as it will give you a better idea of how much you can get from the methodology.
It’s a smart idea not only to go over the most popular ones but also to add those that many companies and individuals are able to obtain through LSS.
This list is important for companies that want to understand how they can go beyond simple growth and improvement with the benefits:
- You get to improve processes.
- All types of waste will be reduced and identified before doing so.
- Improve performance, so processes take less time and employees or workers are more active and productive.
- You can control changes and additions.
- Eliminate bottlenecks.
- Continuous improvement so your company doesn’t fall behind in the industry.
- Customer satisfaction is achieved with Sigma.
- Find the root cause of your problems and then find solutions.
- Strategize based on company goals and requirements
On the other hand, those trained in LSS obtain some additional benefits as they are not based on what the methodology does for companies but rather for them as they learned and got certified in it:
- Career advancement.
- More job opportunities are open.
- Higher salaries.
- All industries are eligible.
- Your curriculum will be more valuable.
- Participate in more projects.
- Students can learn credits towards graduation.
- You will gain hands-on experience in quality management.
- You can work on improving your problem-solving and decision-making skills.
- Leadership skills are learned.
- Assume leadership roles and work in the company of your dreams.
What Makes LSS Crucial for Companies?
People find it attractive that this method was developed using Six Sigma and Lean. This allows you to improve and grow your business as both methodologies are aimed to process improvement and continuous growth.
It can be applied to personal projects by using the principles of both methods. This allows you to create the structure according to your needs and goals.
Six Sigma and Lean have goals that differ from each other, but each leads to process improvement. Lean 6 Sigma, which is a combination of the two methods, was created to compete with the Kaizen method and Japanese manufacturing companies during the 1980s.
LSS is a combination of Lean and 6 Sigma, but it has specifics that make it stand out as a unique methodology. It’s not an imitation of either of them; it is more than just a combination of both.
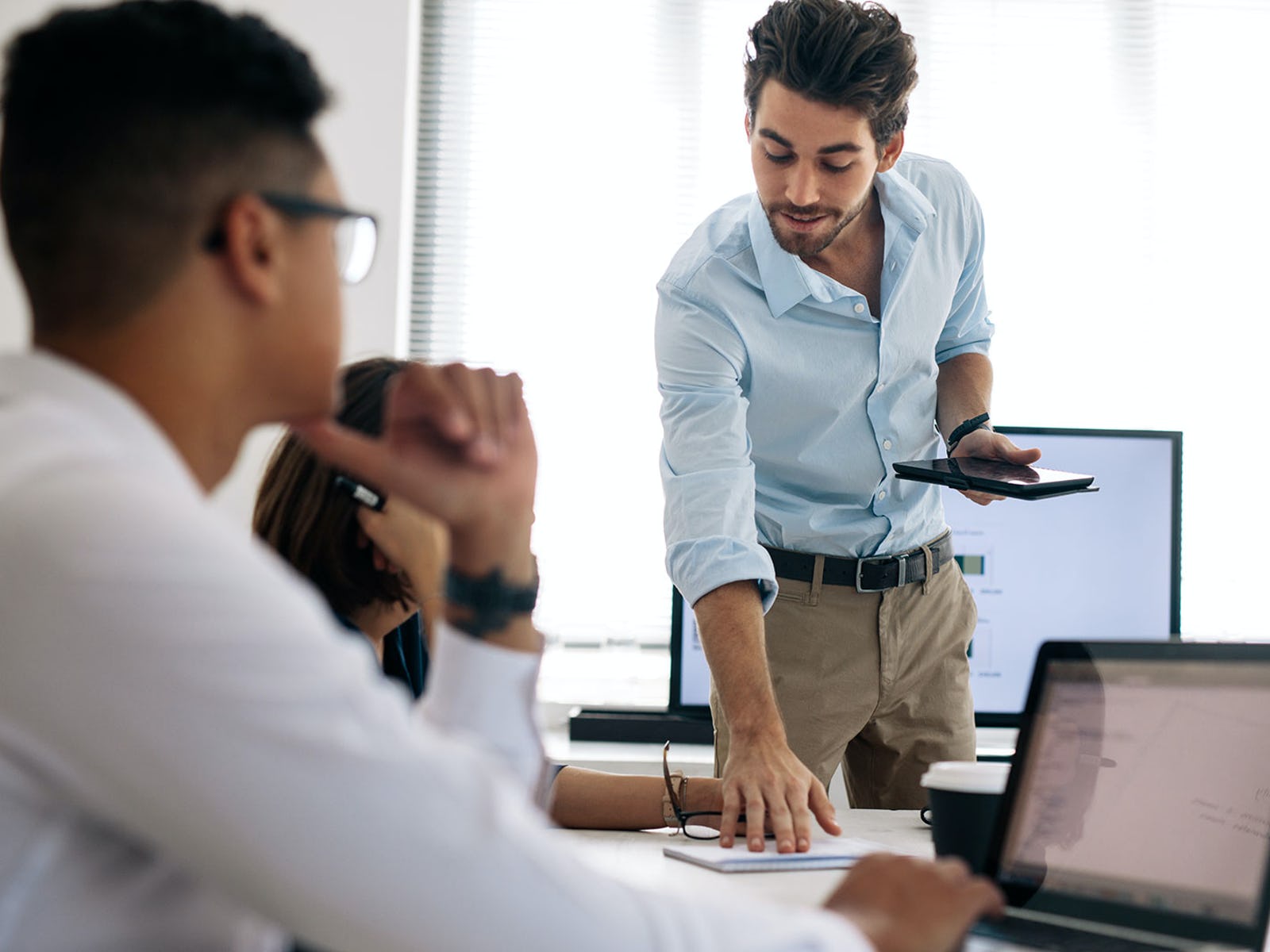
To dive deeper into this entire method, let’s focus on each methodology individually for a bit. Let’s start with Lean because it is the most basic when compared to Six Sigma.
Lean refers to a process of reducing waste. This goal can be difficult for companies that don’t know the nature of waste or people who have never been exposed to it. You can manage both material and physical elements but also intangibles.
This methodology identifies eight types of waste practitioners need to map and identify while also understanding their products.
- Overprocessing.
- Overproduction.
- Motion.
- Defects.
- Waiting.
- Transportation.
- Inventory.
- Talent that isn’t being used
Lean refers to a methodology that employs more tools and methods based on the needs of the person or company.
Six Sigma, on the other hand, is a way to reduce variations and bottlenecks in a company and solve problems. However, if Six Sigma is focused on people, it can help them achieve the goal of not being stuck in one step or process.
Six Sigma is a method to reduce variation and deliver products and services faster. You should remember that it is not connected to Lean 6 Sigma. You can still see the influence of Six Sigma on the waste area.
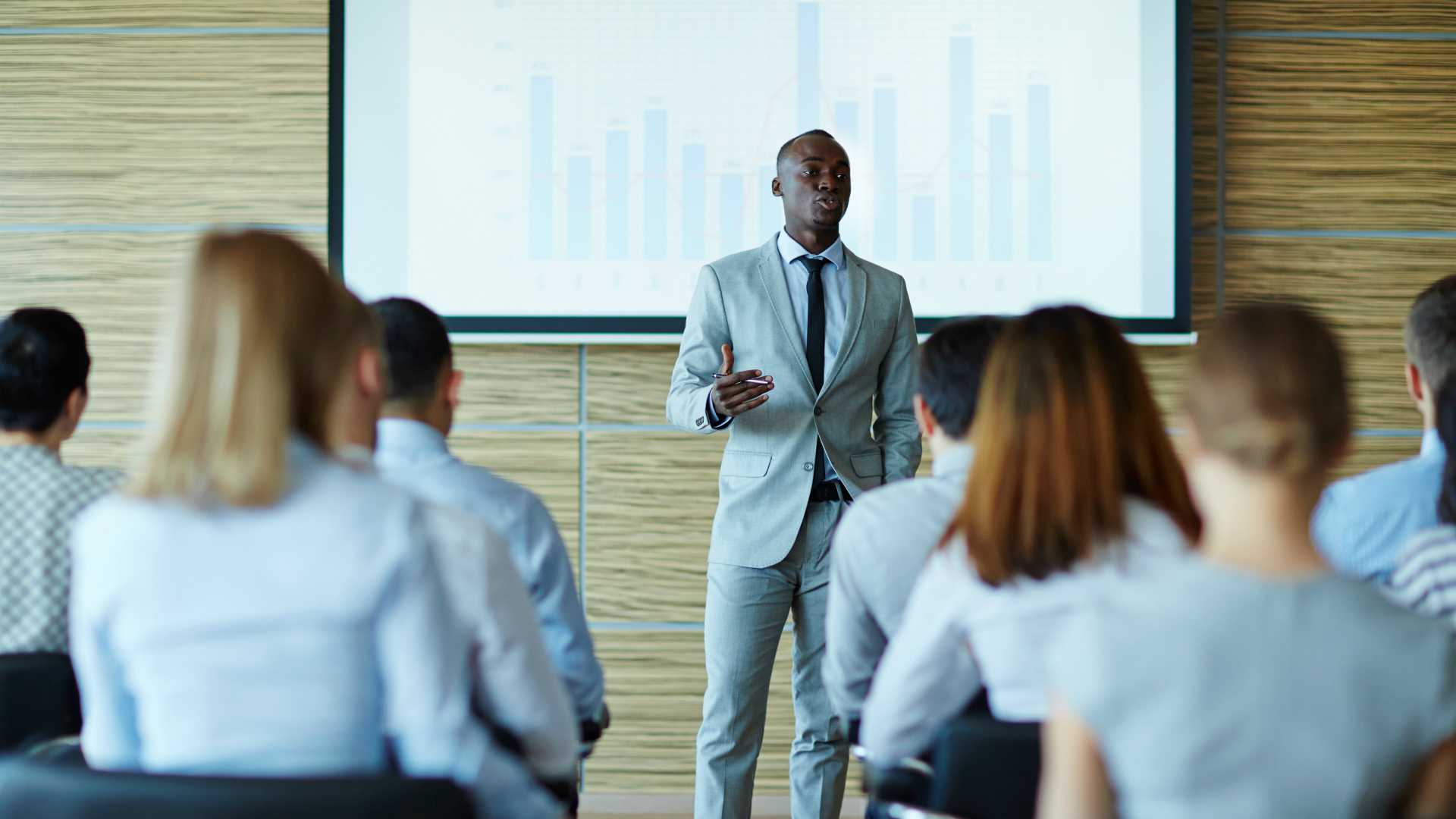
How can Six Sigma help eliminate variation? With a 5-step method called DMAIC: Define-Measure-Analyze-Improve-Control.
It also lists five principles that LSS integrates into its work.
- Concentrate on the customer.
- Find solutions to your problems.
- Reduce variations and bottlenecks
- Employee engagement can be increased
- Flexibility and adaptability.
What Is the Lean Six Sigma Training Program?
Knowing the basics of LSS will help you to plan how to use it in order to achieve your goals and needs throughout high school, college and work. Like other methodologies, Lean 6 Sigma is broken down into levels for learning and training.
Your level of training will affect the course content and outline. Depending on your level of expertise or desired level, topics and skills will vary.
LSS does not consider them “levels” but “belts.” Because colors identify them, LSS offers the main two: Yellow Belt, Green Belt, and their respective certifications.
We at Lean Six Sigma Curriculum Pros of Augusta assist in inculcating the methodology among students and professionals if you are a business or institution looking to provide them with access to the methodology and show them how to grow.
We will guide you according to your life stage and needs. We let everyone know that they have the option to start at the beginning or move on to more advanced training, depending on their goals.
These are the two options that you have in our company:
- Training for yellow belts: This course teaches the basics of Six Sigma terminology and concepts, principles, data collection, key tools, and how to report on problems in projects or processes.
- The training for green belts. This training teaches you how to manage projects, DMAIC and SIPOC main tools, Six Sigma, as well as risk mitigation.
How Long Does Lean Six Sigma Training Take?
The belt you choose will determine the amount of time it takes to train. A yellow belt can be trained in about one to two weeks, while a green belt can take between 2 and three weeks. It will vary depending on how you manage the entire process and the LSS course structure and if you are already a yellow belt to move on with the green one.
While it takes workers in a company a while to learn the new method, it is not difficult for individuals. While our company is simple, we include all the necessary elements of the training. You will be able complete any of our training options quicker than the average person.
A yellow belt takes 7-10 days to complete for anyone who contacts us. A green belt takes 14-20. It can be completed by some in as little as 12 days.
Our team will work with you to create a schedule that works for you or adapt the learning to your students’ availability.
After training, certification is a natural step for all belts. Students will take the exam and become certified, and this will allow them to be recognized worldwide.
Let’s say you’re interested in being certified by our team but haven’t completed the training. You will need to pass the exam with a minimum score—at least—and wait for our team to issue your certificate.
Our Innovation & Leadership Options
We offer more services to help individuals improve their leadership skills and allow them to advance in their careers. We incorporate LSS in the learning process, ensuring that they are fully informed.
Our workshops and innovation consulting help students, workers, and companies to understand the problems with their products and ideas so that they can keep up with the competition and find better solutions.
Consulting will help you assess projects and identify the major issues. This will give you a fresh perspective that can lead to new ideas.
Students will have the opportunity to lead their classmates and teams and bring more value to themselves and the organization.
Contact us to get a detailed look at our services; from high school students and college ones to those who want to make changes in their lives, we are here for you.